The importance of these drill string connections can’t be underestimated — according to reports, a failed connection in offshore drilling can log costs at $250,000 per day.
Cold root rolling, the process of burnishing the root radius of a cut thread in a rotary shouldered connection, has been known to help these drill string connections perform at their best. Studies have shown an increase of three to five times in the joint life of cold root rolled connections, and that’s just the beginning.
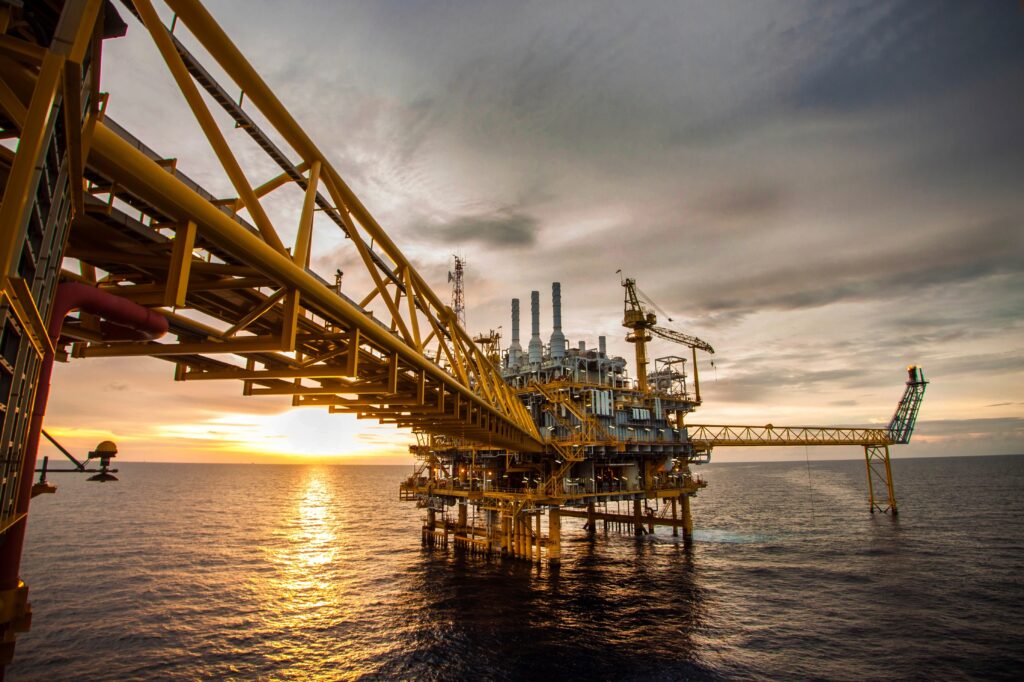
Improved Strength
Cold root rolling is primarily used in offshore drill string assembly, but continues to rise in popularity with on-shore applications. Extended-reach drilling, multi-lateral wells, and horizontal well applications have become more and more common, and these practices all result in a significant stress increase for threaded connections and thus a demand for stronger parts.
The burnishing process of cold root rolling changes the structure of steel material on a fundamental, atomic level. The work-hardening effect on the material surface results in a shift from typical, crystalline steel structure to a dislocated, interlocked steel. The resulting material is less susceptible to shallow cracking and wider structural flaws and damage.
Increased Resistance to Thread Root Stress
Aside from being fundamentally stronger, the rotary shouldered connection that has been cold root rolled distributes stress more effectively. One of the by-products of the process is residual compressive stress, which offsets the tensile stress of service in the crucial regions of a root thread.
“Research has shown that cracks occurring in cold-rolled joints exhibit a considerably low through-thickness crack aspect ratio, typically between 30 to 50 percent longer than unrolled joints.”
Short, deep cracks — more likely than long, shallow cracks after a joint has been cold root rolled — lend themselves to easy detection and repair. This leads to increased chances for a damaged drill string’s recovery before structural failure halts operations.
Reduced Corrosion
Chemical corrosion strikes at scratch points, which provide prime access to steel material for chemicals common in drilling environments. While such chemicals are necessary hazards, cold root rolling smoothes away scratches and imperfections with its burnishing process, reducing access and thus the potential for chemical attack.
More Work In-House
CJ Winter’s cold root rolling tools are simple to use and highly intuitive for machinists. Developed specifically for integration with modern industrial lathes, the benefits of a cold root rolling investment aren’t just vast, they’re easily accessible.
Learn more about the CRR Tool and how to reduce corrosion, costs and downtime with cold root rolling today from the new CJ Winter eBook, The ROI of Cold Root Rolling in Oil and Gas Piping.